纯电折弯机的工作原理基于电能驱动,通过伺服电机和精密机械传动系统,将电能转化为机械能。它利用数控系统精确控制折弯角度、深度和速度。与液压折弯机相比,Electric Press Brake 更环保,能耗更低,精度更高,噪音更小,维护成本也相对较低。它适用于薄板的精密折弯,广泛应用于钣金加工、电子产品制造等领域。控制系统根据预设的程序或操作员的指令,驱动电机带动滑块上下运动,从而实现对金属板材的精确折弯。电机驱动的优势在于控制的精准度和重复性,确保了高质量的折弯效果。
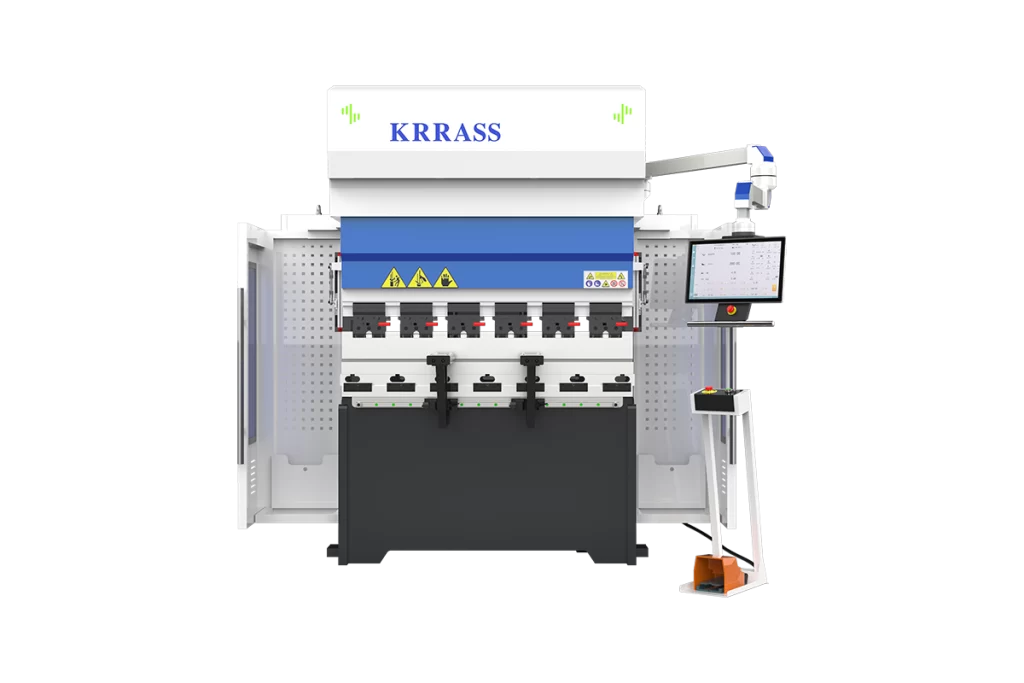
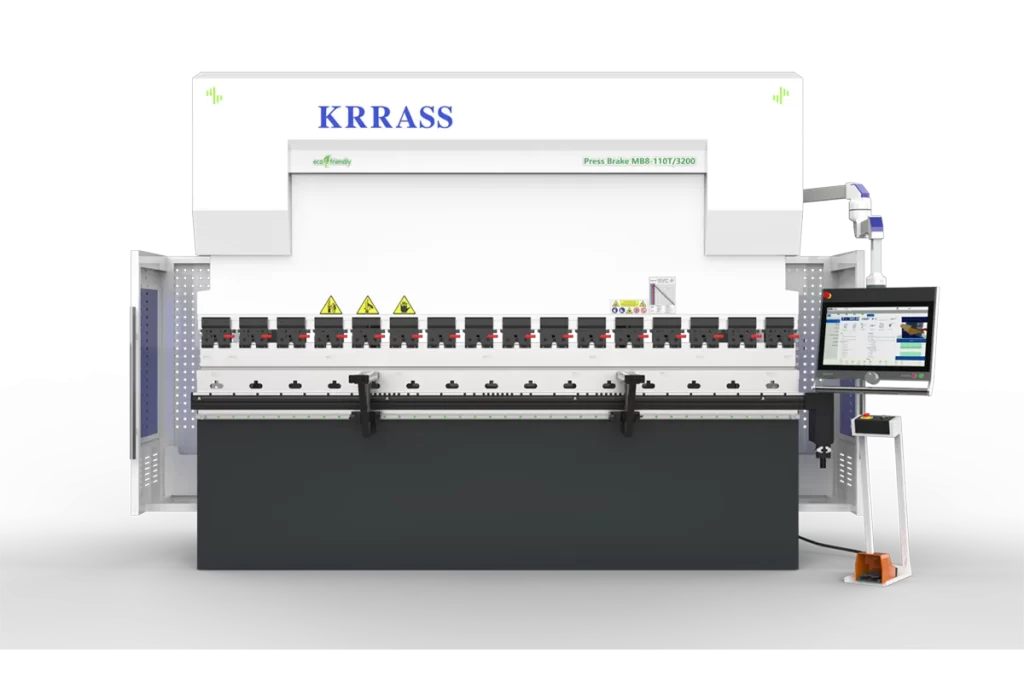
一、纯电折弯机的核心部件: 伺服电机:提供动力源,通过精确控制动力输出,实现折弯过程中的位置和角度控制。伺服电机的高响应速度和精准性是保证折弯质量的关键。
导轨和滑块:确保折弯头或工作台的平稳和精确运动,保证折弯过程中方向和位置的稳定性。
机械传动系统(丝杆、齿轮、同步带等):将电机的旋转运动转化为线性运动,使折弯头上下移动。高精度的传动系统确保折弯角度的准确性。
折弯头:实际进行折弯操作的部分,通过机械夹紧和弯曲金属板材。
控制系统(数控系统):操作界面和智能控制核心,根据预设程序或手动命令控制伺服电机,实现精确折弯。
显示面板/操作界面:方便操作员设置参数、监控折弯状态、调节程序等。
传感器:实时监测折弯角度、位置、压力等参数,反馈给控制系统,用于动态调节和确保折弯精度。
电源系统:供电,确保各个电子元件稳定运行。
二、纯电折弯机的优势: 环保节能:Electric Press Brake 无需液压油,减少油污污染,更加环保。
能耗较低,电机驱动效率高,能有效降低运行成本。
高精度和重复性好:由于采用伺服电机和数控系统,折弯角度、位置和深度可以实现更高的精度。重复折弯的精度稳定,适合批量加工。
操作简便:控制系统人性化,操作界面友好,操作便捷。
具备自动化程序,可实现快速调试和多工序自动操作。
维护成本低:机械结构简单,没有液压系统中的油路、电磁阀等易损件,维护更为方便。
减少油液泄漏带来的问题,延长设备寿命。
噪音低:运行过程中噪音更小,改善工作环境。
响应速度快:
伺服电机具有快速响应能力,折弯速度快,提高生产效率。
安全性更高:电子控制系统具备多重安全保护措施,提升工作安全性。
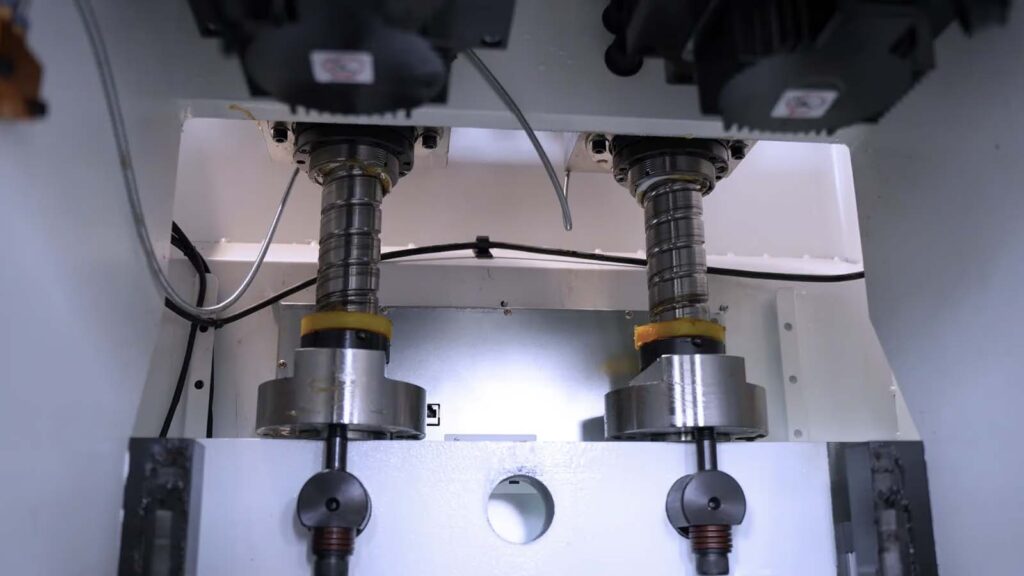
三、伺服电机选型的重要性:
驱动折弯运动:伺服电机为折弯机提供精准的动力,控制上下模或左右模的运动,实现金属板材的折弯操作。这种驱动方式相较于传统液压系统更加灵敏和准确。
高精度位置控制:伺服电机可以实现精细的角度与位置控制,确保折弯角度的精准性,满足复杂或高要求的折弯工艺需求。
实现快速反应与调节:由于伺服系统具有高速响应能力,可以在折弯过程中快速调整模具位置和压力,提高生产效率及折弯质量。
能量回收与节能:在某些设计中,伺服系统可以回收运动过程中的能量,降低能耗,提升整体能效。
简化机械结构和维护:使用伺服电机替代液压系统,减少了液压油和油路的复杂性,降低了维护成本和设备故障风险。
四、优化纯电折弯机策略:
1. 选择高性能驱动元件
伺服电机:选用响应速度快、扭矩稳定的伺服电机,确保运动的精准性和动态响应能力。
传动机构:采用高刚性、低间隙的传动部件,如钢丝绳、滚珠丝杠、同步带或齿轮传动,减小传动误差。
2. 采用精密的传动结构
滚珠丝杠:具有高效率和高精度,有助于实现平稳、精准的运动。
同步带或链条:用于长距离传动时,提高传动效率和耐用性。
线性导轨:保证运动路径的直线性,减少偏差。
3. 设计合理的减速装置
使用高效减速器,确保扭矩传递稳定同时降低能量损耗。
选择合适的齿轮比,兼顾速度与扭矩需求。
4. 强化刚性和减震措施
结构设计上增强刚性,减少振动和变形。
在关键部位增加阻尼结构,减缓运动过程中的振动。
5. 集成闭环控制
利用编码器和传感器实现反馈控制,实时调整运动参数,确保折弯角度的精准性。
采用先进的控制算法(如 PID、Model Predictive Control 等)优化运动轨迹。
6. 优化润滑与维护
定期润滑传动部件,减少摩擦和磨损。
设计便于维护的结构,便于检测和更换关键零部件。
7. 数字化仿真与测试
通过 CAD/CAM 软件进行运动仿真,提前评估传动系统的性能。
在实际设计前进行动力学分析,优化传动参数。
五、纯电折弯机丝杆的选型?
纯电折弯机的丝杆选型需要综合考虑设备的负载特性、精度要求、运动参数及结构设计等多方面因素,以下是详细的选型流程及关键要点:
一、明确丝杆选型的核心参数
1. 负载分析
轴向负载:由折弯力决定,需计算最大折弯力通过机械结构传递到丝杆的轴向力(Fₐ)。
例:若折弯机最大压力为 100kN,机械传动效率为 80%,则丝杆轴向负载 Fₐ=100kN/80%=125kN。
径向负载:由滑块、模具等运动部件的重量及偏心载荷引起,需避免丝杆因径向力产生弯曲变形。
动态负载:加速 / 减速时的惯性力(F=ma),需考虑滑块质量(m)和最大加速度(a)。
2. 精度要求
定位精度:折弯机对工件的折弯角度精度通常要求 ±0.5° 以内,对应丝杆的定位精度需达到 0.01~0.05mm/1000mm(如 C7 级滚珠丝杆)。
重复定位精度:影响工件一致性,建议选择重复定位精度≤±0.005mm 的丝杆。
3. 运动参数
最大速度(v):由生产效率决定,如滑块最大下行速度通常为 100~200mm/s。
加速度(a):影响动态响应,一般取 500~1000mm/s²,高速机型需更高。
导程(P):导程越大,速度越高,但扭矩需求也越大,常用导程为 10~20mm。
六、丝杆类型选择:滚珠丝杆 vs 梯形丝杆
类型 | 优点 | 缺点 | 适用场景 |
滚珠丝杆 | 效率高(90%~95%)、精度高、寿命长 | 成本高、对安装精度要求高 | 高精度、高速 Electric Press Brake |
梯形丝杆 | 成本低、结构简单 | 效率低(30%~60%)、磨损快 | 低精度、低速或小型折弯机 |
建议:Electric Press Brake 优先选择滚珠丝杆,因其能满足高精度和高效率需求。
1. 确定丝杆直径(d₀)
- 根据轴向负载 Fₐ,参考滚珠丝杆的额定动载荷(Cₐ)公式:Ca=Fa×31000L×fw×fh
其中:- L 为预期寿命(mm),一般取 100 万~500 万 mm;
- f_w 为负载系数(冲击负载取 1.5~2.5);
- f_h 为硬度系数(滚珠丝杆硬度≥58HRC 时取 1)。
- 示例:若 Fₐ=125kN,L=300 万 mm,f_w=2,则 Cₐ=125×√[3]{3000}×2≈125×14.4×2=3600kN,需选择额定动载荷≥3600kN 的丝杆(如直径 63mm、导程 20mm 的滚珠丝杆)。
2. 验算临界转速与稳定性
- 临界转速(n_c):避免高速运转时共振,公式为:nc=L2997×d02
其中 L 为丝杆支撑间距(mm),需确保实际转速 n < n_c(一般取 n < 0.8n_c)。 - 轴向稳定性:长径比(L/d₀)较大时需验算屈曲载荷,避免丝杆受压弯曲。
3. 匹配电机与传动比
- 电机扭矩(T):计算公式为:T=2π×ηFa×P+Tf
其中 η 为丝杆效率(滚珠丝杆取 0.9),T_f 为摩擦扭矩(约为 0.1~0.2 倍负载扭矩)。 - 传动比(i):若电机最大转速为 n_m,需满足:i=v×60nm×P
例:v=150mm/s,P=16mm,n_m=3000rpm,则 i=3000×16/(150×60)=5.33,可选 i=5 的减速比。
4. 精度等级与预紧方式
预紧方式:双螺母预紧可消除间隙,提高刚性,适用于高精度场景;单螺母无预紧成本低,但存在间隙。 精度等级:按 ISO 标准,C5~C7 级适用于一般折弯机,C3 级适用于精密折弯机。
七、结构设计与安装要点
支撑方式:
1.一端固定 + 一端支撑(结构简单,适用于中短丝杆)。
润滑与防护:
2.滚珠丝杆需定期涂抹锂基润滑脂或使用自动润滑系统;
加装防尘罩(如波纹管、钢带罩),防止粉尘进入影响寿命。
热膨胀补偿:长丝杆需考虑温度变化引起的伸长,可通过预拉伸安装或预留补偿间隙
八、选型案例参考
- 机型:100 吨 Electric Press Brake,工作台长度 3 米,定位精度 ±0.03mm。
- 丝杆选型:
- 类型:轧制滚珠丝杆(成本低于研磨丝杆,满足一般精度);
- 直径 × 导程:50mm×16mm;
- 精度等级:C7 级;
- 支撑方式:两端固定 + 双螺母预紧;
- 电机匹配:伺服电机功率 7.5kW,减速比 i=4,最大转速 2000rpm,满足滑块速度 133mm/s。
九、注意事项
- 负载波动:折弯过程中负载非恒定,需按最大负载选型,并考虑安全系数(1.5~2 倍)。
- 刚性匹配:丝杆刚性需与机架、滑块刚性协调,避免因丝杆变形导致精度下降。
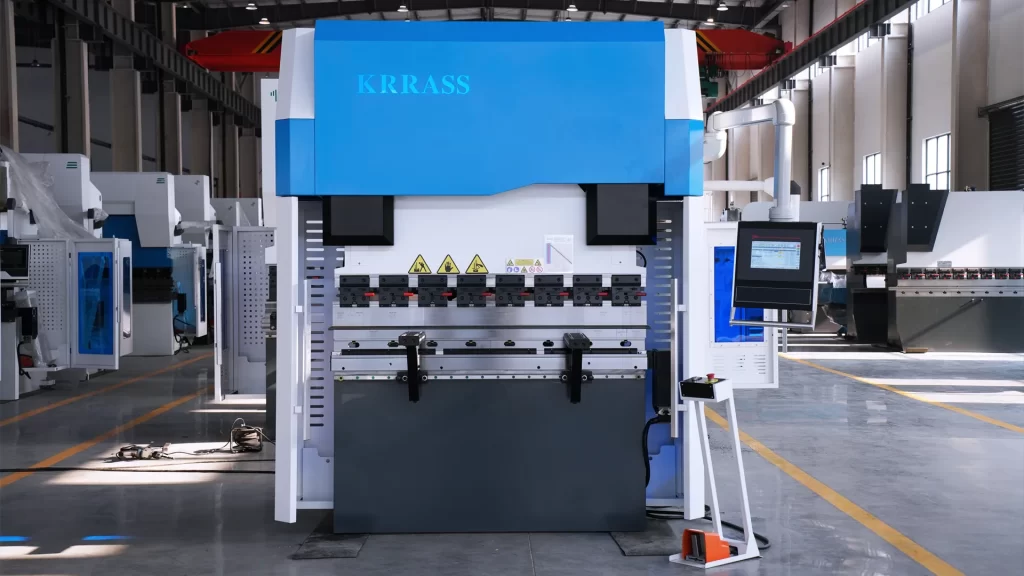
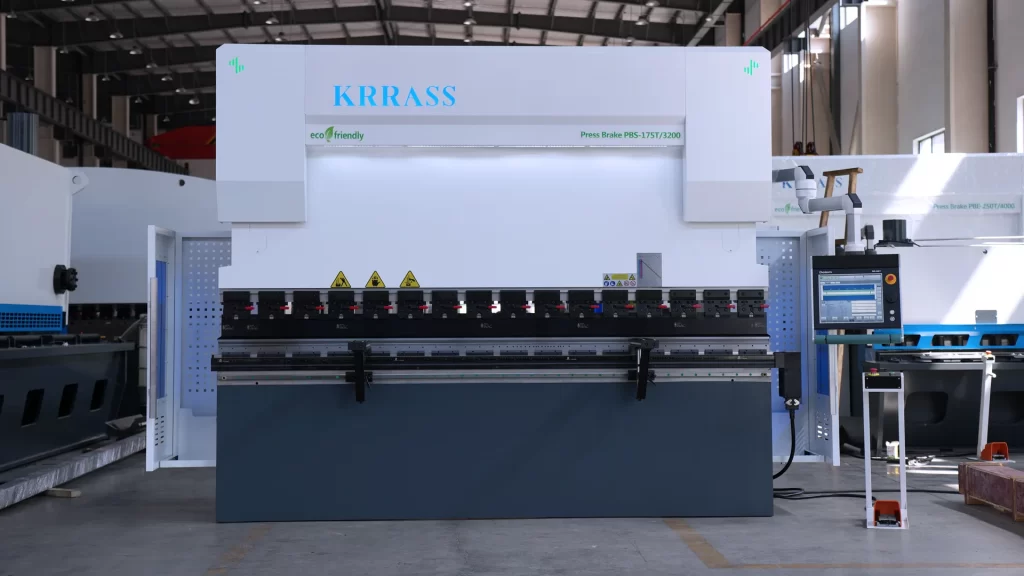
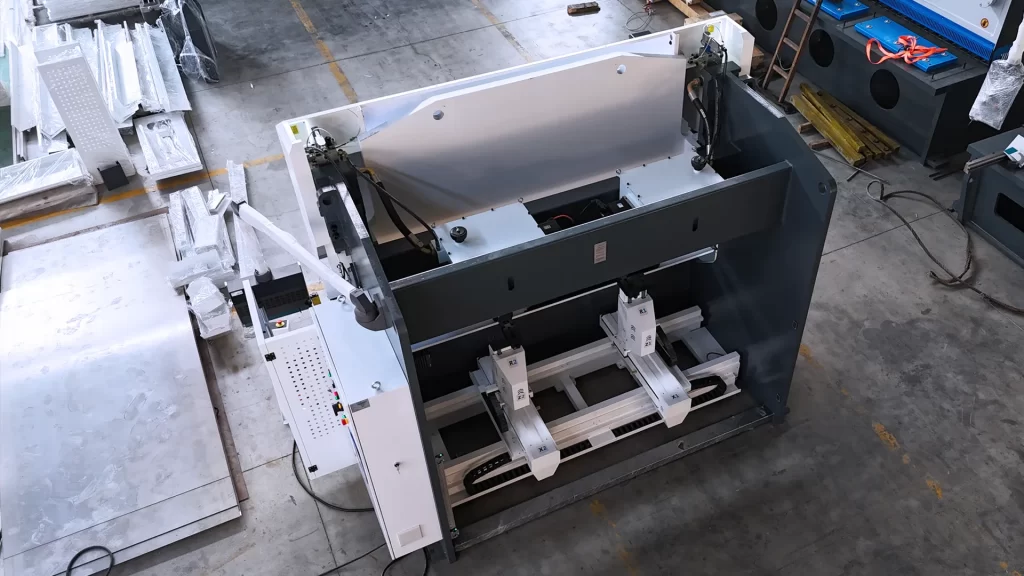